The new equipment of spin flash dryer adopts a variety of devices, such as a variety of feeding devices, so that the feeding is continuous and stable, and the feeding process will not cause bridging phenomenon; the bottom of the dryer adopts a special cooling device, which avoids the occurrence of materials in the high temperature area at the bottom The phenomenon of sticking to the wall and deterioration; special air pressure sealing device and bearing cooling device are adopted to effectively prolong the service life of the transmission part
The new equipment of spin flash dryer adopts a variety of devices, such as a variety of feeding devices, so that the feeding is continuous and stable, and the feeding process will not cause bridging phenomenon; the bottom of the dryer adopts a special cooling device, which avoids the occurrence of materials in the high temperature area at the bottom Sticking to the wall and deterioration phenomenon; using special air pressure sealing device and bearing cooling device, effectively prolonging the service life of the transmission part; using special air distribution device, reducing equipment resistance, and effectively providing the processing air volume of the dryer; the drying room is installed There are grading rings and swirl sheets, which can adjust the fineness and final moisture of the material; the stirring and pulverizing device is used to produce strong shearing, blowing, and rotating effects on the material; the air filter, cyclone separator, bag filter, etc. Effectively remove dust and avoid environmental and material pollution. The equipment has strong mass and heat transfer, high production intensity, short drying time and short material residence time. So today, an experienced drying equipment manufacturer in Changzhou will introduce to you the four major process design methods of spin flash dryer!
1. Determination of the drying room
The evaporation intensity of some materials treated by the spin flash dryer, and the volume heat supply method is the theoretical design method of the spin flash dryer, but the key volume heat supply coefficient in this method is difficult to determine, so it lacks operability. The evaporation intensity method is an indirect method of the volume heating method. It can be calculated as long as there are certain experimental data. It is a method often used in industrial design. The evaporation intensity method calculates the volume of the drying chamber according to the amount of evaporated water and the evaporation intensity, and then calculates the effective height according to the relationship between the diameter and the height.
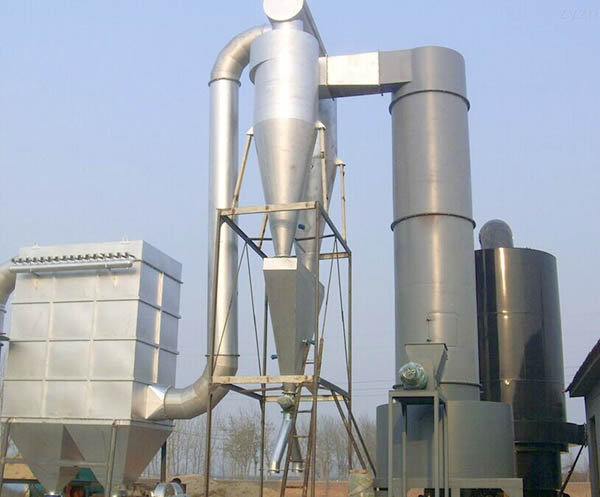
2. Diameter of drying chamber
Another method is to calculate the required air consumption through material balance and heat balance, and then determine the diameter of the dryer according to the air speed range.
3. The height and graded particle size of the dryer
The hot air from the hot air distributor enters the drying chamber tangentially through the annular gap, and the materials in the drying chamber make a spiral rotating upward movement under the action of the hot air blowing and the push of the agitator. When studying the fluid motion of smaller particles under the action of centrifugal force field, the effect of gravity is very small, so it can be ignored.
4. The application of spin flash dryer
The operating conditions of some rotary flash dryers. The upper part of the drying chamber is provided with a grading ring, which is mainly used to separate the materials with larger particles or not dried from the qualified products. Blocking in the drying chamber can effectively ensure product particle size and moisture requirements. Replacing grading rings with different diameters can meet product particle size requirements. The hot air inlet at the bottom of the cone is provided with cold air protection to prevent the material from overheating and deterioration due to contact with high temperature air. The drying system is closed, and it operates under a slight negative pressure, so that the dust does not leak out, which protects the production environment and is safe and hygienic.
Post time: Sep-04-2023