At present, the glaze spray powder in my country's glass-lined equipment industry is mainly divided into two categories: cold spray (powder) and hot spray (powder). Most of the enamel equipment manufacturers in the north generally use the cold spray technology, while the glass-lined equipment manufacturers in the south mostly use the hot spray technology.
1. At present, the glaze spray powder in my country's glass-lined equipment industry is mainly divided into two categories: cold spray (powder) and hot spray (powder). Most of the enamel equipment manufacturers in the north generally use the cold spray technology, while the glass-lined equipment manufacturers in the south mostly use the hot spray technology. Let's talk about the difference and advantages and disadvantages of hot and cold powder spraying.
2. The biggest advantage of the thermal spray technology in the south is that the cost is very low, and the enamel process can often be produced two or three times. However, the disadvantage is that the quality is unstable, and the product is prone to problems in inferior environments, resulting in more losses for users.
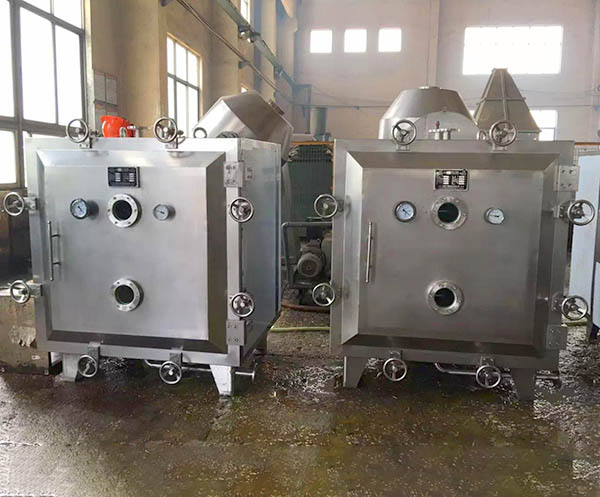
3. The biggest advantage of the cold spray technology in the north is that the product quality is stable, but the enamelling process of the equipment is about six to seven times, so the cost is too high. You know, every time you add enamel, it has to be fired at a high temperature of thousands of degrees, which shows that the cost gap is huge.
The quality of the enamel equipment is not only related to the quality of the enamel, but also has an important relationship with the spraying technology selected for the enamel equipment. To put it simply, cold spraying is a powder spraying operation performed on the blank of the enamel equipment when it is cooled and at room temperature, while thermal spraying is a powder spraying operation performed when the blank of the enamel equipment is in a working state before being completely cooled. Cold spray is convenient for workers to grind and refine steel billets and porcelain powder again and again, and the moisture in the porcelain powder is naturally dried. The porcelain layer under this technical operation is thin (large effective thickness), and the number of firing times is large. High; thermal spraying is performed when the enamel equipment is not completely cooled, and the water in the enamel powder is forced to dry through the uncooled steel plate, so the cycle is fast and the output of the equipment is large. Also because of the temperature problem, thermal spraying can only Covering each production defect cannot be finely ground, so the porcelain layer of the enamel equipment is relatively thick and the cost is relatively low.
4. It can be seen that although the thermal spray technology produces fast and the porcelain layer is thick (the enamel equipment is not the thicker the porcelain layer, the better), but due to the high temperature operation, it is easy to produce dark bubbles, the porcelain is thick and uneven, and the entire porcelain surface is easy to fall off. Although the cost of cold spray is high and the production volume cannot be expanded, from the user's point of view, the production equipment is guaranteed, and the porcelain layer is uniform (in line with international standards).
Post time: Sep-04-2023